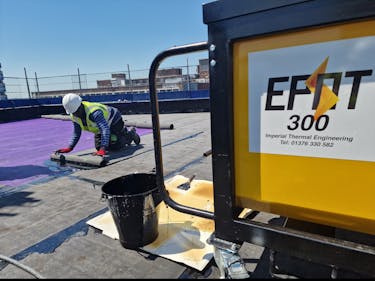
We recently tested the very latest version of the Epot system, alongside Axter’s Wilotekt® Plus second-generation hot melt waterproofing system, at a residential project in Southampton.
Traditional methods of waterproofing that rely on liquefied petroleum gas (LPG) and open flames can present challenges in certain environments.
In contrast, flame-free technologies like the Wilotekt® Plus system, paired with the Epot system from Imperial Thermal Engineering – an all-electric replacement for the gas bitumen boiler – provide a safer alternative that eliminates the risk of fire while maintaining efficiency and effectiveness.
The transition to flame-free methods represents a vital step in reducing workplace accidents and fostering a culture of safety across the industry.
We recently tested the very latest version of the Epot system, alongside Axter’s Wilotekt® Plus second-generation hot melt waterproofing system, at a residential project in Southampton. Both the contractor and roofing installer were impressed by the quick, stress-free, safe, and cost-effective installation.
The Epot system: Electric power and flame-free safety
The Epot System by Imperial Thermal Engineering – developed in partnership with Wilotekt® Plus –addresses the safety concerns inherent in traditional LPG-powered systems. Originating from a need to eliminate fire risk, the Epot was developed to operate without an open flame, using electrically charged components instead.
This approach has proven highly effective; the recent project in Southampton illustrated its advantages in terms of operational safety, efficiency, and reduced maintenance compared to LPG-driven alternatives.
Operatives on site highlighted several benefits:
Using the Wilotekt Rubberised Compound in conjunction with the Epot has resulted in smooth and precise application. The system is fantastic, delivering outstanding results with ease.
The efficiency of the Epot system has increased our productivity. We no longer need to monitor it constantly, freeing up time for additional projects. Its standby option is particularly useful, allowing us to maintain a consistent temperature overnight. The separate bucket burner compartment has streamlined the cleaning process, removing the need for manual flame cleaning
We appreciate the safety features of the Epot system, such as the heated bars for adding hot melt blocks, which have been well-received. The elimination of gas cylinder checks and replacements has greatly simplified our operations
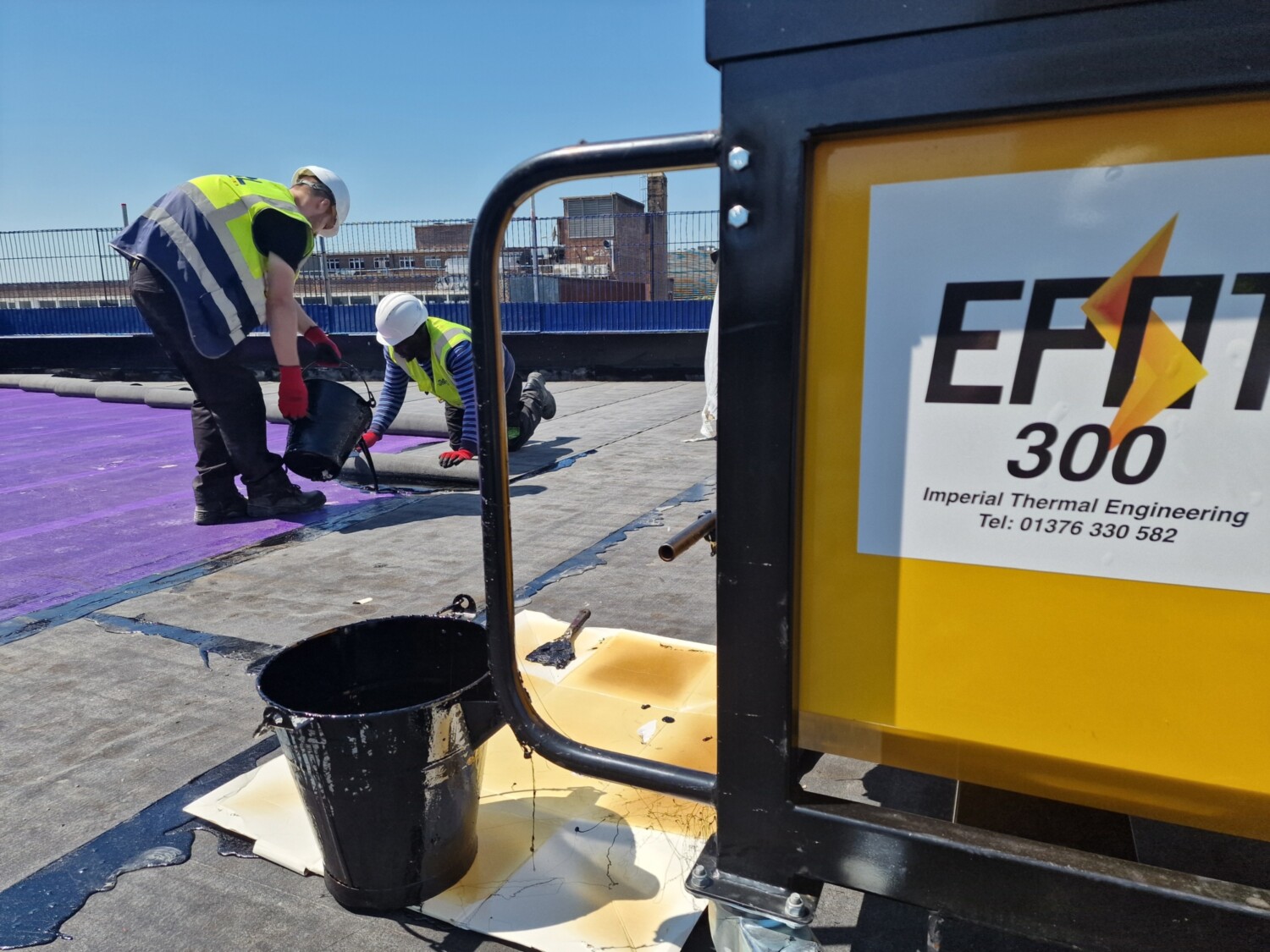
The Epot VS conventional LPG tooling with Wilotekt ®-Plus: Safety and efficiency
In the Southampton test project, the Epot and conventional LPG-powered bitumen pots were put to the test side by side and compared across several key areas. The absence of a flame eliminates fire hazards, addressing a primary health and safety concern. A combination of the unique low-melting-point of the Wilotekt® Plus compound with the electric Epot system, meant the operatives experienced a smooth, consistent application with no performance drop-off. The Epot also outpaced the traditional LPG tooling in terms of efficiency, providing an overall quicker and more seamless waterproofing process.
To reinforce this observational testimonial with a controlled test, quantitative data and independent third-party assessment, Axter and Imperial Thermal Engineering are in the process of collaborating with third-party consultants to conduct an evidence based carbon and cost analysis of the Epot versus LPG with Wilotekt-Plus.
Wilotekt® Plus: A legacy of reliability
The perfect partner for the Epot, Axter’s Wilotekt® Plus brings over two decades of trusted performance with a minimum 35-year guarantee and an impressive record of zero failures. The simplicity, robustness, and longevity of Wilotekt® Plus have made it a preferred choice among contractors, installers, and clients alike.
Embracing electric innovations for a safer, sustainable future in waterproofing
As the construction industry shifts toward safer and more efficient, eco-friendly and cost-effective solutions, Axter’s Wilotekt® Plus used in conjunction with the Epot system illustrates what the future of flat roof inverted hot melt waterproofing will look like. Taking a well-established and loved product with a proven track record, and boosting this with advanced electric tooling means these systems will soon become the new standard in structural waterproofing, paving the way for a safer, greener future in construction.
By shifting away from traditional gas-fuelled equipment and embracing electric-powered alternatives, contractors and suppliers can realise efficiencies, improve safety, and lower their environmental impact. Worker health and safety has always been and remains at the forefront of Contruction design excellence; adopting flame-free technologies is a necessary evolution for the industry.
If you are interested in speaking with our expert team at Axter to find out how we can help you with your flat roofing project, please contact us on 01473 724056 or email [email protected]; a member of our team would be happy to speak with you.