Oxford
The Cheng Yu Tung Building, Jesus College
Projects of complexity that demand innovative solutions to technically challenging interface design often deliver exceptional buildings. As a shining example, Axter recently completed the roofing systems for The Cheng Yu Tung Building, a landmark project for Jesus College in the heart of Oxford City.
- Client
- University of Oxford
- Project type
- New Build
- Project sector
- Education
- Accredited Installer
- Briggs Amasco Ltd - Birmingham
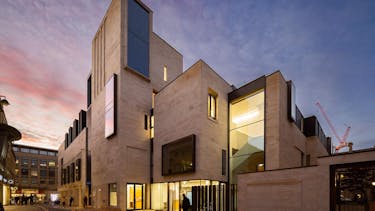
Systems in use
-
Starcoat® PMMA
A flame free and rapid cure, two component polymethyl methacrylate (PMMA) resin waterproofing system that provides a fully adhered waterproofing layer.
-
Force Dalle®
The first of its kind, Force Dalle is an innovative hybrid waterproofing system that combines the benefits of hot melt systems and advanced polymer modified bitumen membrane technology to create a unique and highly durable system that is a cost effective alternative to traditional hot melt.
-
Excel®
A premium range of high performance reinforced bitumen waterproofing membranes, manufactured with the unique Alpa polymeric binder, making it our most technologically advanced RBM system.
-
Cityflor®
Cityflor warm roof living roof systems are robust SBS polymer modified bitumen membranes for use in extensive and intensive green, biodiverse brown and modular green roofs, as well as protected terrace, podium and balcony applications.
Overview
This project required Axter’s extensive range of materials and methods combined to complete the multifaceted interfaces and deliver the demanding architectural design, whilst achieving the project’s ambitious goals.
Founded in 1571, and with original buildings from this date, Jesus College is based in the centre of this diverse and historic city. With the development of the Cheng Yu Tung Building the college has undertaken its most significant transformation since the early 18th century.
Combining new graduate accommodation, indoor and outdoor communal spaces, state-of-the-art teaching and meeting facilities with the latest digital technologies, this £36m innovative development is intended to have significant impact on the college faculty and students’ learning experience.
Axter worked with architects MICA from early in the process, helping to specify solutions that would realise the design vision of lead architect Mandy Franz.
“We’d worked with MICA before on a number of projects - including Keble College, University of Oxford - so they knew us and trusted us to add value through being involved with the design,“ comments Axter's Regional Sales Director, Matthew Saunders. “However, this project was a significant step up in complexity, with approximately 18 separate roof areas in total to complete. Looking at the main quad alone there is a raised area, numerous external stairways and walkways to waterproof as well as further raised terraces and inaccessible roof sections. Fortunately, we had significant experience to bring to this challenge.”
Sustainability was the client’s major focus from the start, with the college already utilising ground source heat pumps, photovoltaic panels, and a heat recovery and cooling system to ensure zero carbon building operations, as well as reviewing all construction waste to ensure minimum diversion to landfill. We supported this aim working with main contractor BAM Construct UK to carefully plan and schedule the waterproofing systems to be installed, identifying the material composite of each roof to maximise efficacies in installation and logistics.
The College’s key priority was to achieve a sustainability-focused design to reduce their carbon footprint. Naturally, this contributed to the challenges of the scheme, such as the additional fire safety requirements in response to the timber-framed construction. To help deliver the College’s ambitions, Axter supported the client’s design team by providing expert knowledge, understanding and application of the current regulations.
Tapered roof insulation was used to support energy efficiency and drainage requirements, with bituminous waterproofing throughout. In keeping with the college’s sustainability mission, the main quad features a blue roof system to attenuate rainwater drainage. Other roof areas are finished with wildflower meadows. A combination of exposed and buried waterproofing membranes were consequently required, with additional complexity created by the range of different materials and surfaces involved.
“Normally, if our membrane is marrying up to a vertical wall, we would see it come up as a visible detail,” continues Matthew, “but the beautiful Clipsham stonework used for the building façade wasn’t compatible with the typical detailing. We were also challenged by the desired architectural intent to defend the historic aesthetic of the stone, so we created a bespoke solution that has the required guaranteed watertightness whilst also delivering the architectural vision.”
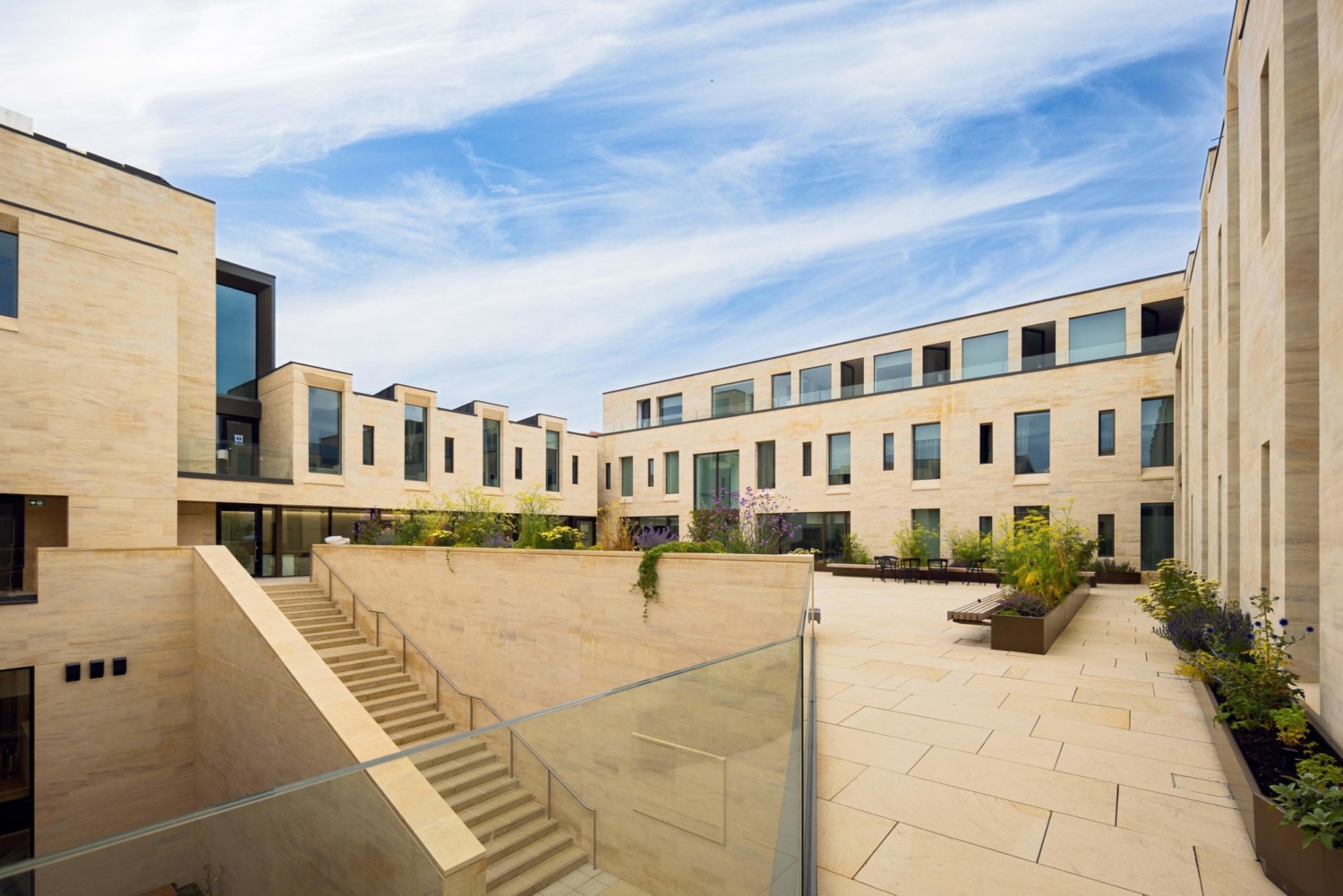
Additional challenges
The project started in 2020, just as the UK was trying to navigate the guidelines for operating during the COVID-19 pandemic. Matthew explains: “there were still restrictions in place, such as a general 2-metre distancing requirement, which was challenging in the tighter spaces, for example corridors where you literally couldn’t pass another person. We had an unusually hot summer also, which wasn’t helpful when you have workers in full PPE using 1,400-degree butane torches where use of naked flame was permitted in accordance with NFRC Safe2Torch guidance.”
The overall scope of the project, which encompassed multiple terraces at different levels and a mixture of concrete, CLT and steel frame structural composites, was a defining characteristic. “This was a large-scale development to begin with,” adds Matthew. “Furthermore, the university emphasised from the start the centrality of the significant sustainability objectives, and MICA had ambitious solutions in mind in terms of the materials used. Our job was to accommodate these various requests while keeping in mind all of the regulatory and compliance requirements. Achieving those without exception, for a large number of surfaces, does become more challenging where each part of the project has several ambitious aspirations intersecting with one another. Fortunately, we are known for always rising to a challenge.”
Solutions
The pandemic accelerated the shift to a range of technological solutions replacing traditional or face-to-face approaches. Systems were evolved for everything from distancing to digital rather than traditionally signed delivery acceptance.
“As a manufacturer, we don’t have to be on site every day,” notes Matthew, “but traditionally we would attend fairly frequently, as well as meeting regularly with partners to agree and then oversee various aspects of the project plan. Fortunately, Axter was already moving towards solutions such as virtual meetings, so we simply shifted much more quickly to those approaches, using them wherever possible.
“I think one advantage we have is the breadth of the product range we design. We can offer clients such as Jesus College a full system approach involving multiple solutions, to ensure we use the right system for the right application on each occasion. Our accredited installers are carefully vetted and trained by us, and have worked with us for long enough to know our products inside out.”
The range of products we are able to offer, all developed in-house, does testify to the culture of Axter. Comments Matthew: “We are very much a technically-oriented company and that runs through every aspect of our work and our staff. Our sales team are all very aware of the products on that level, they aren’t selling products they don’t fully understand the technical details of. Our long-term partners know that what we offer them is reassurance that, from early-stage design meetings through to completion, whatever challenges they put to us, our response will be considered and robust in terms of quality and compliance.”
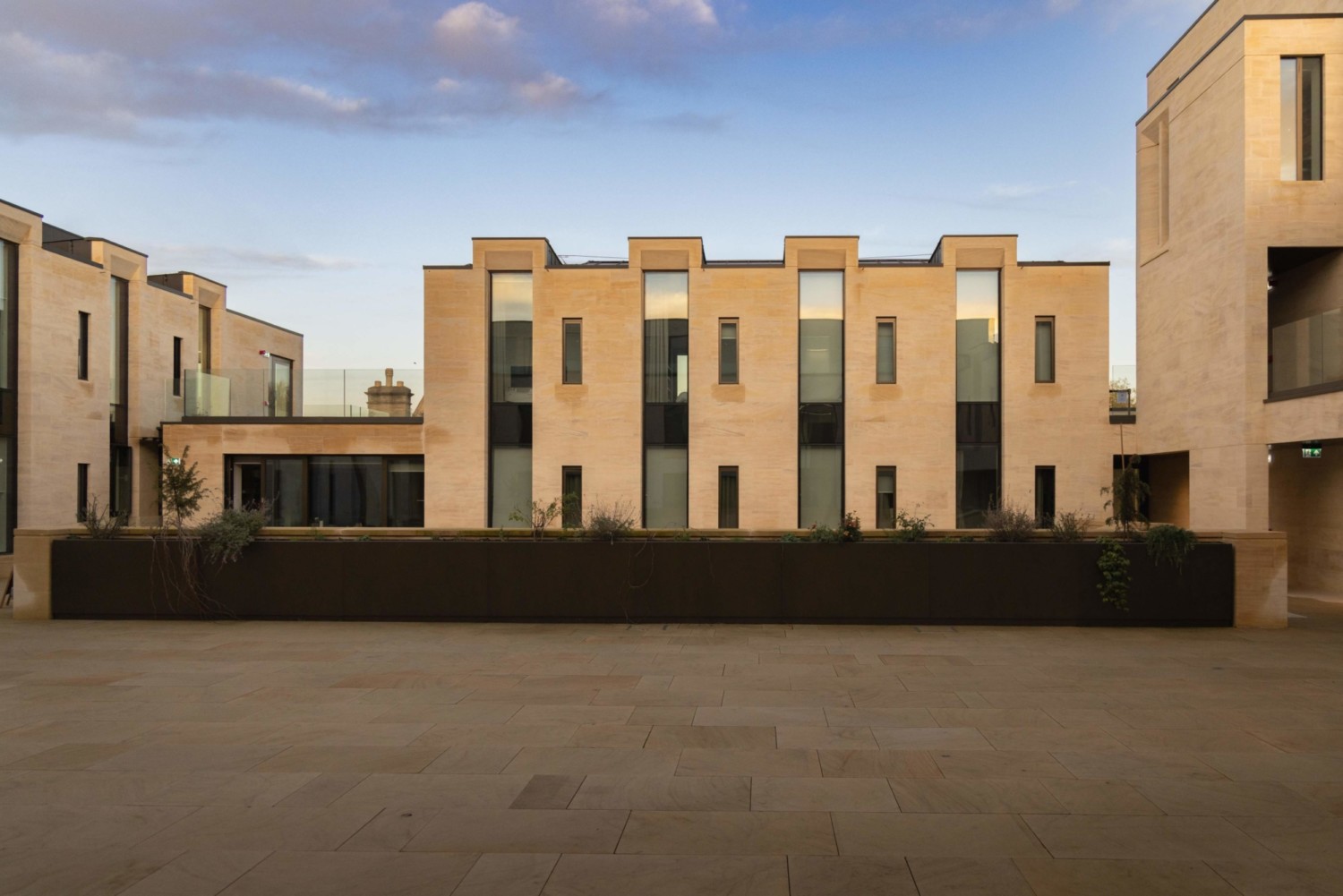
Systems and products used
External stair cores used Axter Starcoat PMMA liquid waterproofing membranes.
For the main quad and some lower areas, our innovative Force Dalle warm roof solution was used.
Our Excel reinforced waterproofing membranes were used as an exposed membrane finish, with a tapered insulation to ensure the falls and consequent drainage characteristics required by BS 6229.
Axter’s Cityflor warm living roof membranes were used as buried applications in several roof terraces, again with tapered insulation.
Self-adhesive membranes were used where necessary to ensure compliance with NFRC Safe2Torch Guidelines, especially required due to the timber elements.
To deliver the increasing demand on a building’s performance specification, combined with the seamless aesthetics of contemporary architectural design, an advanced understanding of technical detailing is required in the design and construction process. The design criteria have also resulted in an extensive range of engineered systems on the market to provide certified, technical solutions for multifaceted interfaces.
Eric O’Hare, Design Manager, BAM Construction www.bam.co.uk
Working directly with the designers and product manufacturers, we prioritise a full system approach to the weather-tightness of the building, focusing on durability, termination and compliance with current regulations. I have worked with the team at MICA Architects and Axter’s Matthew Saunders on a number of challenging projects, including The Cheng Yu Tung Building, Jesus College, and the HB Allen Centre, Keble College. Matthew Saunders has always been a key consultant for the technical specification of above ground waterproofing systems and the buildings’ thermal performance. He’s an expert in technical detailing and advisor on the materials required to deliver the optimum waterproofing system for the building.
With special thanks to: Tomasz Zozak, who provided the photographs, and BAM Construction Ltd.