London
West End Gate, London
Flexibility and innovative bespoke designs have been needed for a major and ongoing project which is now entering a new phase. Find out how we are supporting long-standing partner Berkeley Homes throughout COVID and price fluctuations, plus unexpected regulatory and design changes, as they seek to add almost a thousand homes to central London.
- Client
- Berkeley Homes (Central London) Limited
- Project type
- New Build
- Project sector
- Residential
- Accredited Installer
- Fenland Flat Roofing Limited,
- Hambro Roofing Limited
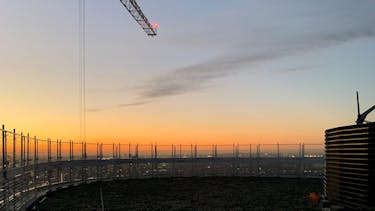
Systems in use
-
Wilotekt®-Plus
The original and industry renowned second generation hot melt system. Unique structural waterproofing designed and manufactured for use on all inverted roofs, podium decks, living roofs, blue roofs and car park decks.
-
Force®
A superior range of high performance SBS polymer modified reinforced bitumen membranes. Engineered to guarantee durability, Force self protected systems have exceptional ageing characteristics and a proven track record of excellent performance.
-
Force Dalle®
The first of its kind, Force Dalle is an innovative hybrid waterproofing system that combines the benefits of hot melt systems and advanced polymer modified bitumen membrane technology to create a unique and highly durable system that is a cost effective alternative to traditional hot melt.
-
Aquamodul®
The Aquamodul blue roof sustainable drainage system is designed to attenuate, control and manage rainwater at source, providing attenuation capacity within the flat roof or podium deck construction of a development that can be combined with living roof, Solar PV and multi-functional mixed amenity finishes.
Overview
Berkeley Homes initially contacted Axter in early 2017 about their project to create 844 apartments (including 175 affordable units), plus 8 shops, a restaurant, and a public plaza. The development, located in Edgware Road, will bring prosperity and jobs as well as housing, to a part of London in need of regeneration.
The development involves 11 apartment blocks and is divided into 4 phases. Axter were involved in design prior to works starting, and were subsequently awarded the contract for Phase 1, later expanded to include Phase 2 and the current Phase 3.
This is an update to a project we initially wrote about in its first phase. As noted there, Phase 1 was complicated by the fact that the Government amended the Building Regulations in 2018, after design work was completed and approved, imposing stricter requirements in relation to combustible materials in high-rise buildings. Timing meant that the developer was permitted to proceed under the old regime, but elected to apply stricter safety standards including a voluntary change to the system used on the balconies that was both tested to BRoof(t4) and included non-combustible insulation. The Axter team had to work quickly to amend designs but were able to modify the approved solution so that work could continue as scheduled.
Phil Saunders, Regional Sales Director at Axter, has been our lead throughout the work. “This is one of the most challenging projects I have worked on,” he notes, “but also one of the most rewarding. Unique solutions were required to solve more than one problem, but it has been great to work on a development involving many technically elegant and aesthetically pleasing aspects, with a range of roofing systems and finishes, including Blue, Brown and Green Roof elements.”
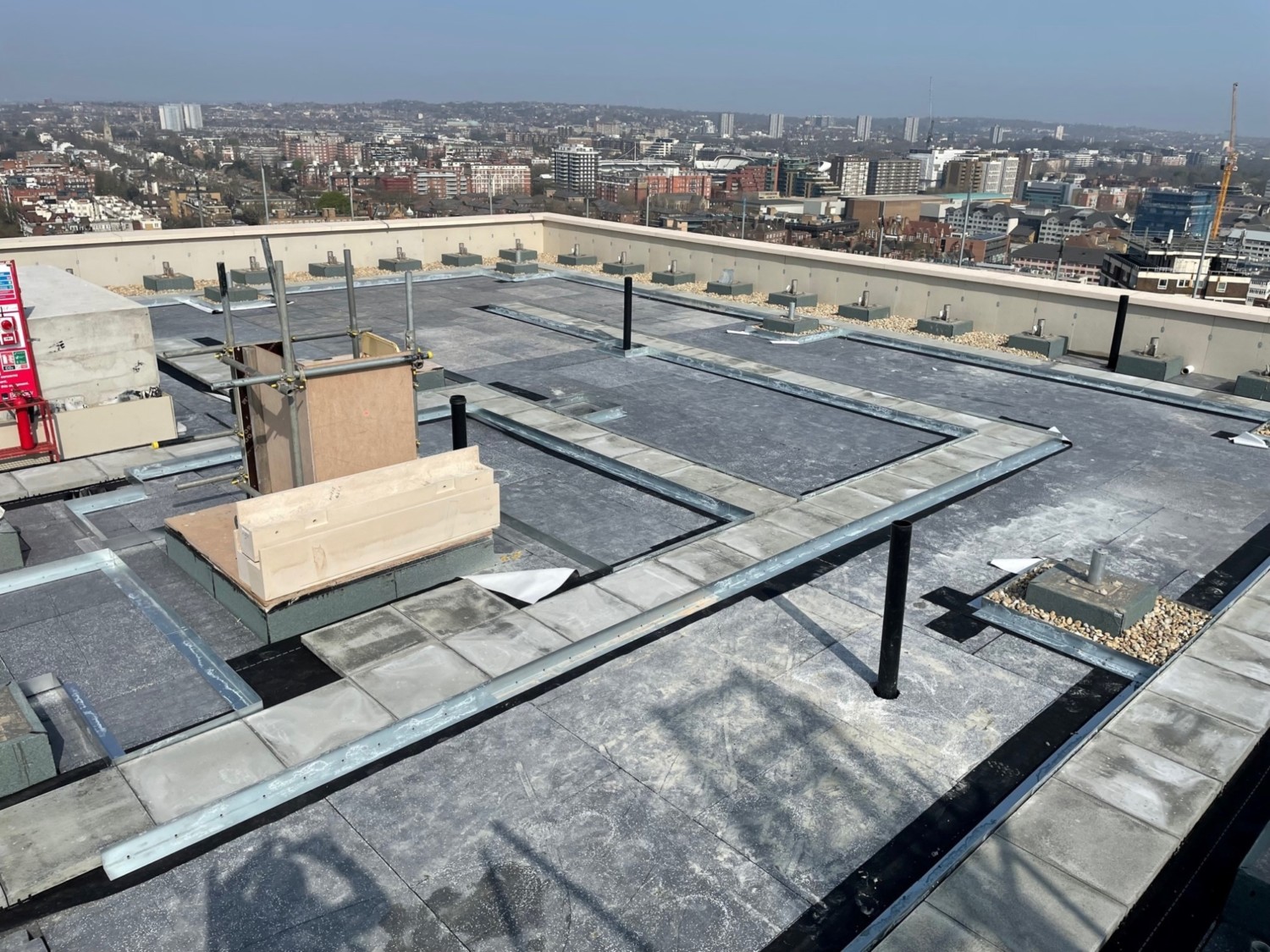
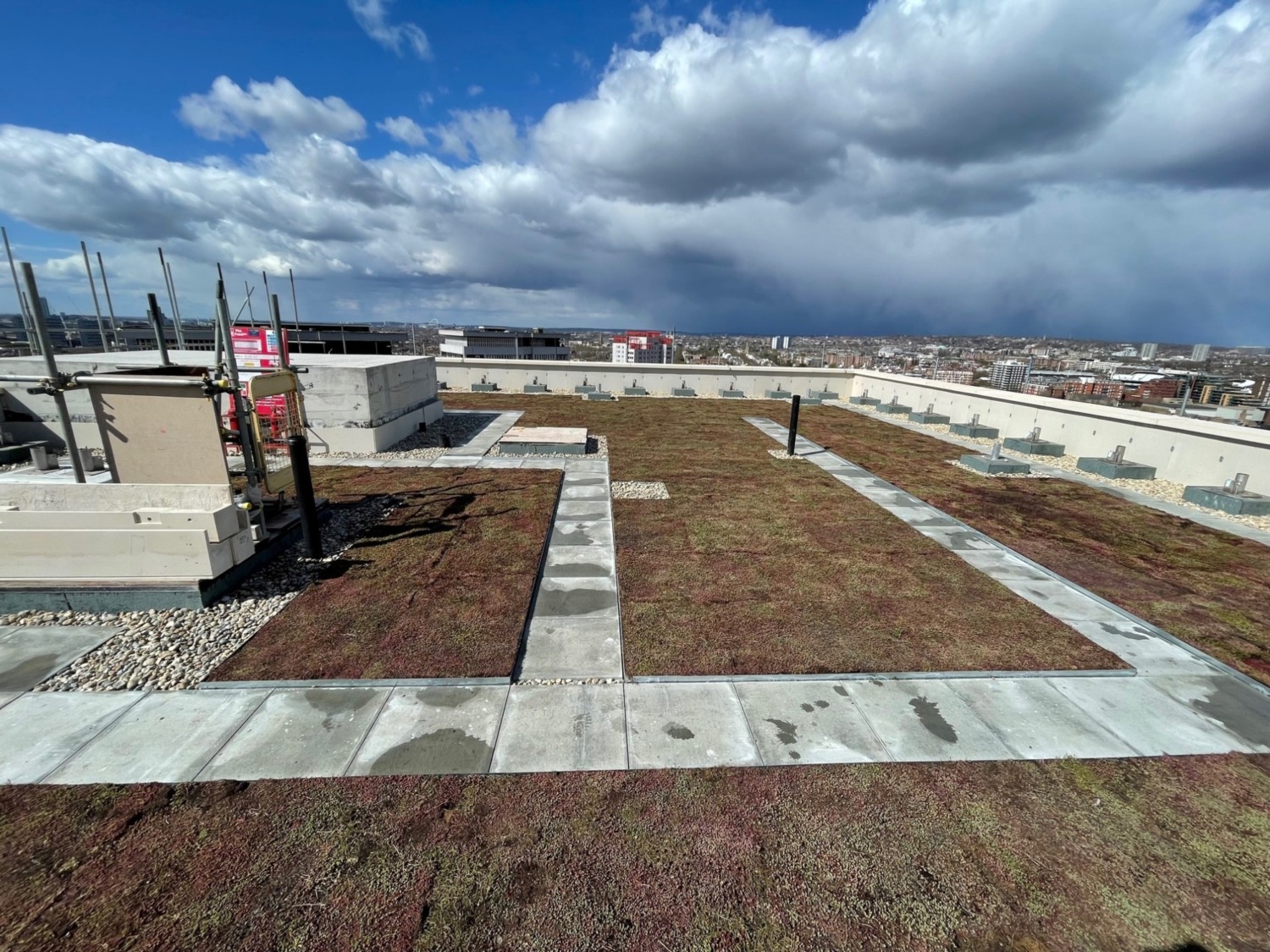
Additional challenges
Westminster Council’s planning requirements included specific stormwater attenuation targets. With limited space onsite, Kevin Leahy, Technical Director at Berkeley Homes, was considering a Blue Roof solution, something the developer had not implemented before, so support from a technical manufacturer was especially important from the outset.
Numerous other difficulties have had to be overcome during this project. Work was disrupted by Covid lockdowns not long after roofing commenced in 2019. Phases 2 and 3, which were very similar, also required us to support our partner through complex change: Phase 1 involved an inverted roof, a solution assumed to carry forward. However, assessment of weight restrictions and outlet positions meant that design would need to switch to a warm roof with tapered insulation.
Additionally, work has continued throughout the period of the Ukraine conflict, where prices and supply of materials have been difficult to navigate.
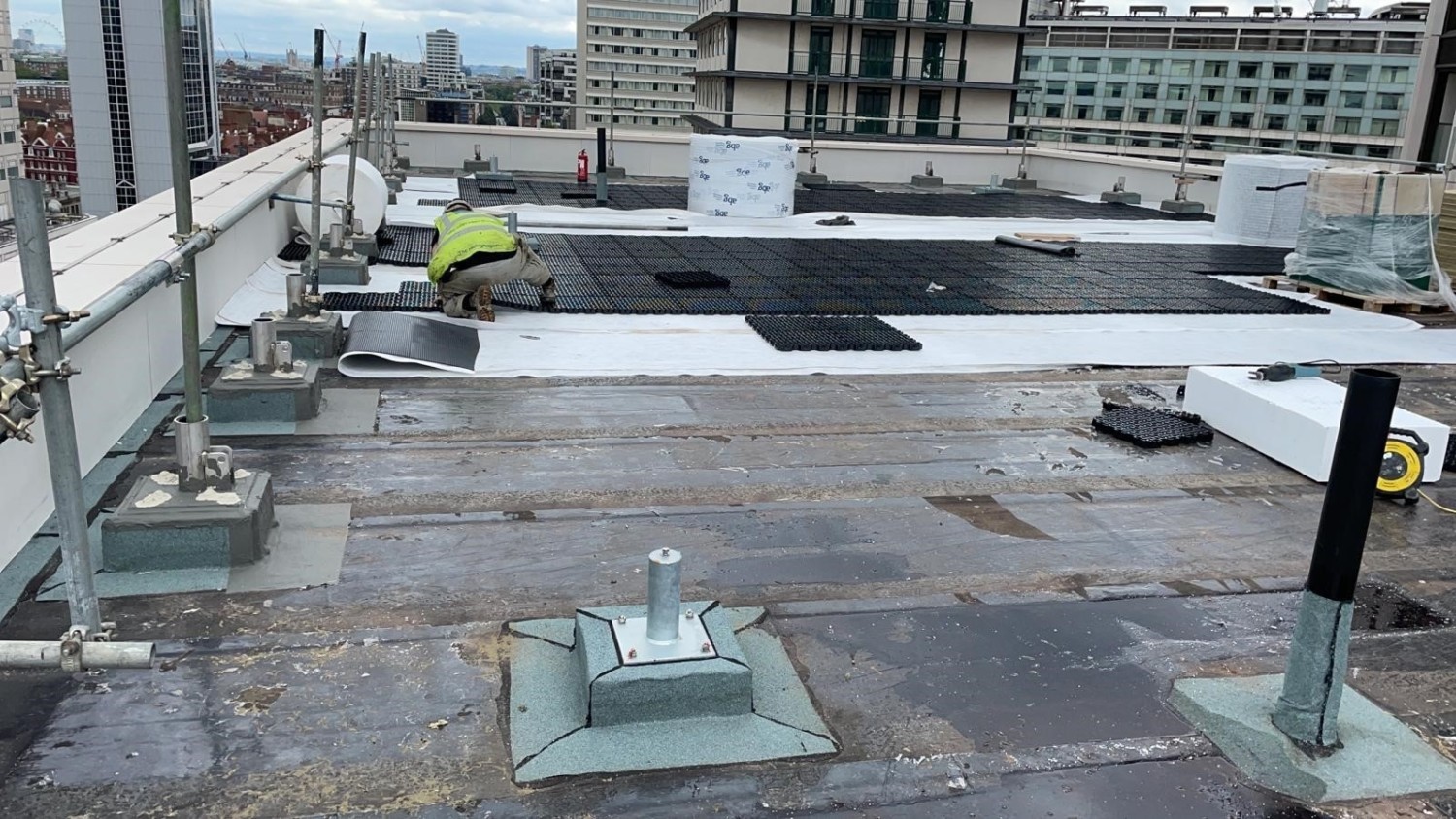
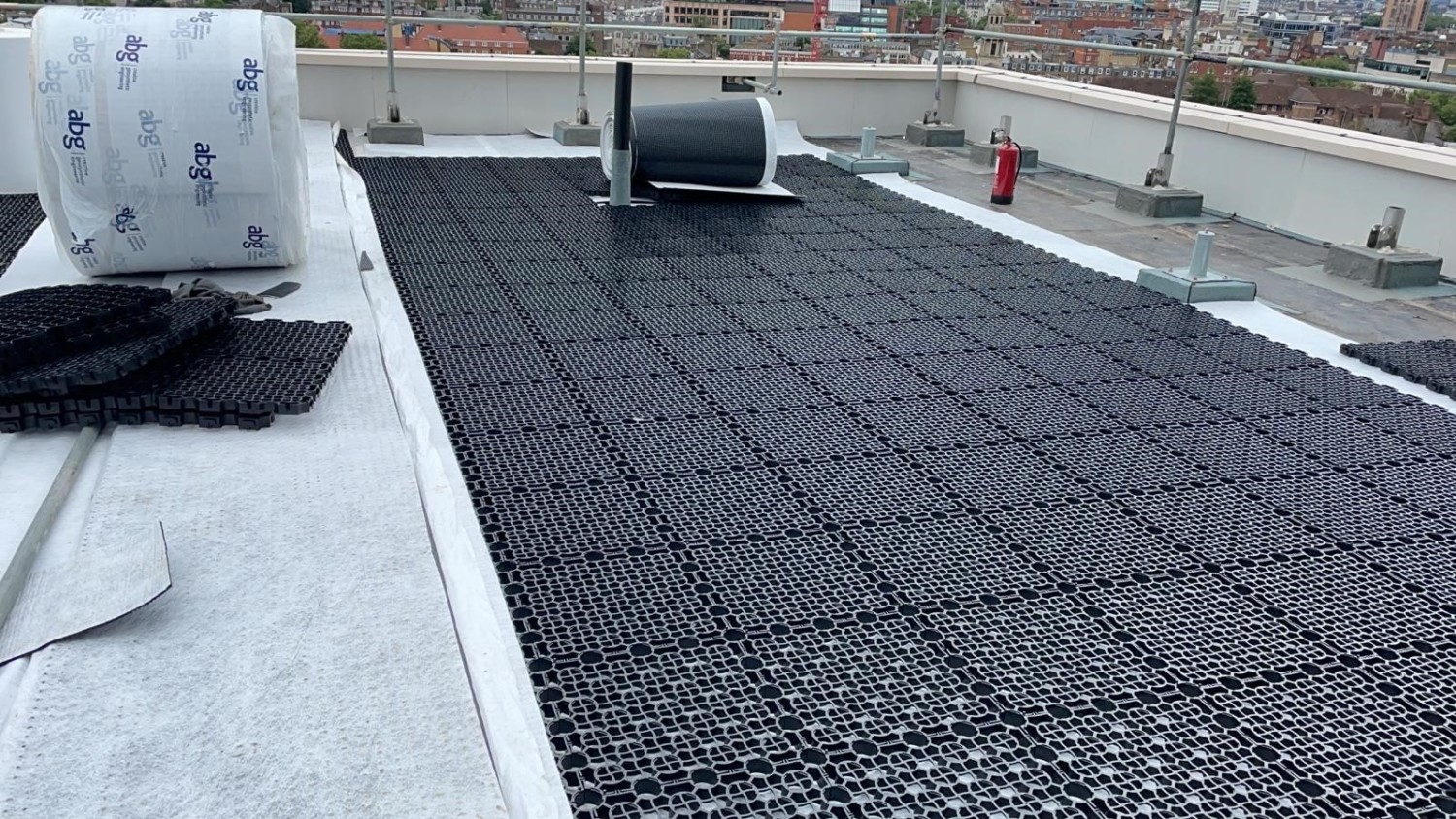
Solutions
To achieve planning permission, Axter worked with Kevin and Berkeley Homes between 2017 and 2019, presenting the resultant roofing design for approval. We were able to demonstrate that the plans met sustainable drainage obligations. The London Plan for sustainable design and construction also imposed requirements, which were met by a mix of living roof solutions including Green Roof and Brown Roof finishes.
“We’re happy to present Westminster Council to support the planning application,” continues Phil. “We have worked with Berkeley Homes many times and continue to do so on several projects. Nothing matters more to us than building and maintaining ongoing relationships with partners who know they can trust us to take weight from their shoulders.”
Construction continued throughout the lockdown period, with Axter working hard to ensure uninterrupted supply. Materials continued to be delivered in a safe manner, and QA reviews were held virtually until we could resume our usual regular site visits.
A switch in roofing approach generally changes the sequencing of work such as integration of roofing and door thresholds. “We were able to come up with an innovative solution involving multiple systems, including cold-applied liquid waterproofing, that permitted the original sequencing to remain,” says Phil. Change was also required in relation to upstand penetration details and movement joints.
Throughout the project, Axter has been able to provide partners with full designs involving bespoke details, plus rainwater and u-value calculations, to ensure compliance at every stage.
“We worked hard to find the smartest, most cost-effective solutions,” adds Phil. “We also appreciated that this was not the time to be too rigid in pricing. Some pain all round might be unavoidable in this difficult period, but we aimed to share the impact. We were also able to offer partners a guarantee of price stability for a set period of time, so they could proceed with certainty.”
Axter manufactures its own systems and works carefully to plan ahead and liaise with long-standing supply partners. This allows us to stay ahead of shortages and offer accurate delivery timelines. Company-wide, we have been able to supply all systems as pledged.
All of Axter’s approved installers must complete training specific to the systems involved, but in this case so many bespoke design elements were involved that we organised training specific to the project for all operatives. This training was also extended to the Berkeley Homes construction team, to ensure they were supported in how the roofing would integrate with other areas of construction.
“This has been an exceptionally successful project”, comments Phil. “Hurdles have arisen, but with communication and hard work we have supported our client through rapid transitions and financial challenges. We have been very flexible on pricing, but we were not necessarily the cheapest initial bid. We were chosen anyway, because I think Berkeley Homes understands we add value that makes us the cost-effective option for the building’s future lifetime.”
Phase 3 designs were approved early this year, with work just starting. Axter is now busy with design for Phase 4, with the project expected to continue through to 2025.
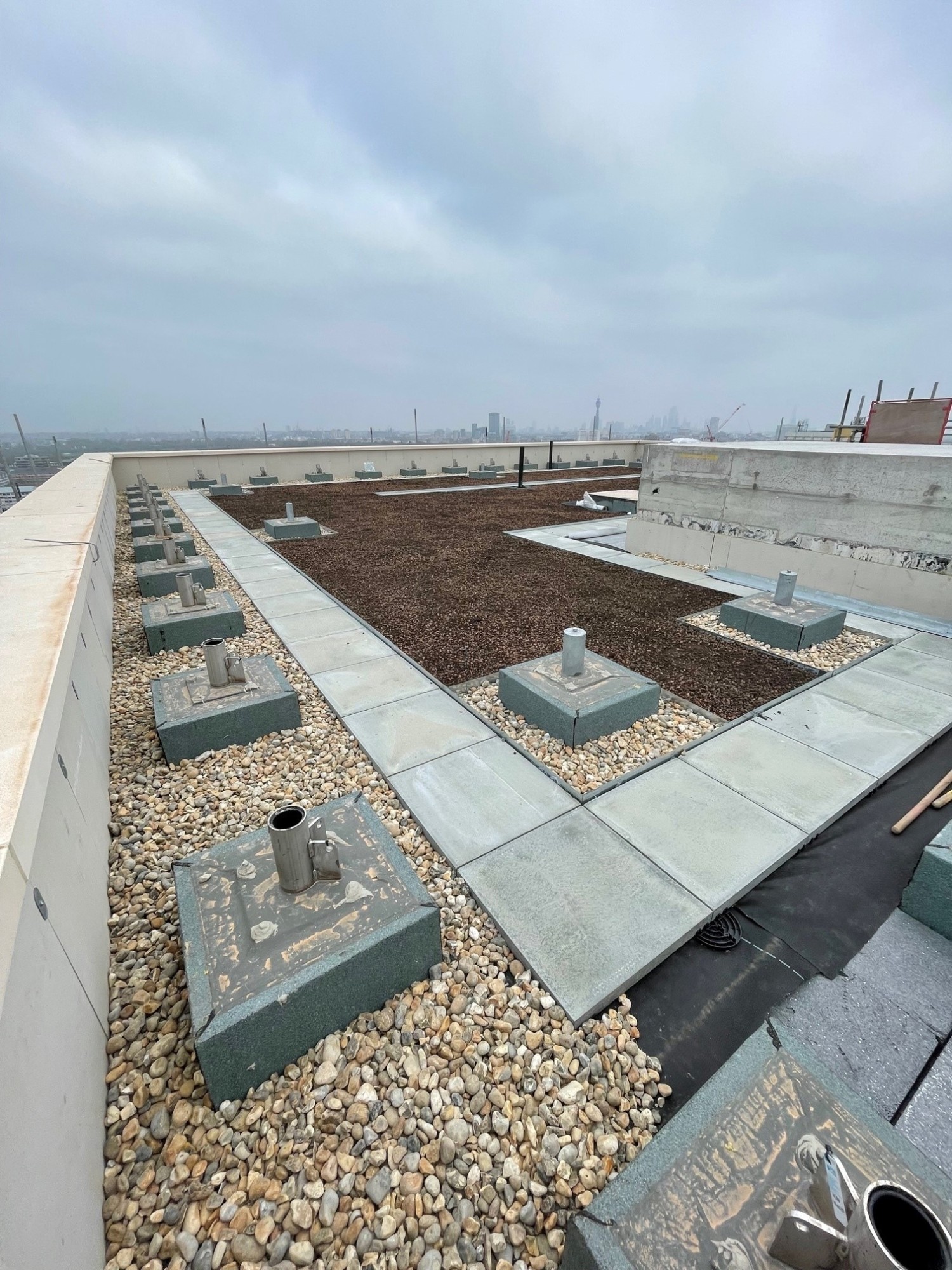
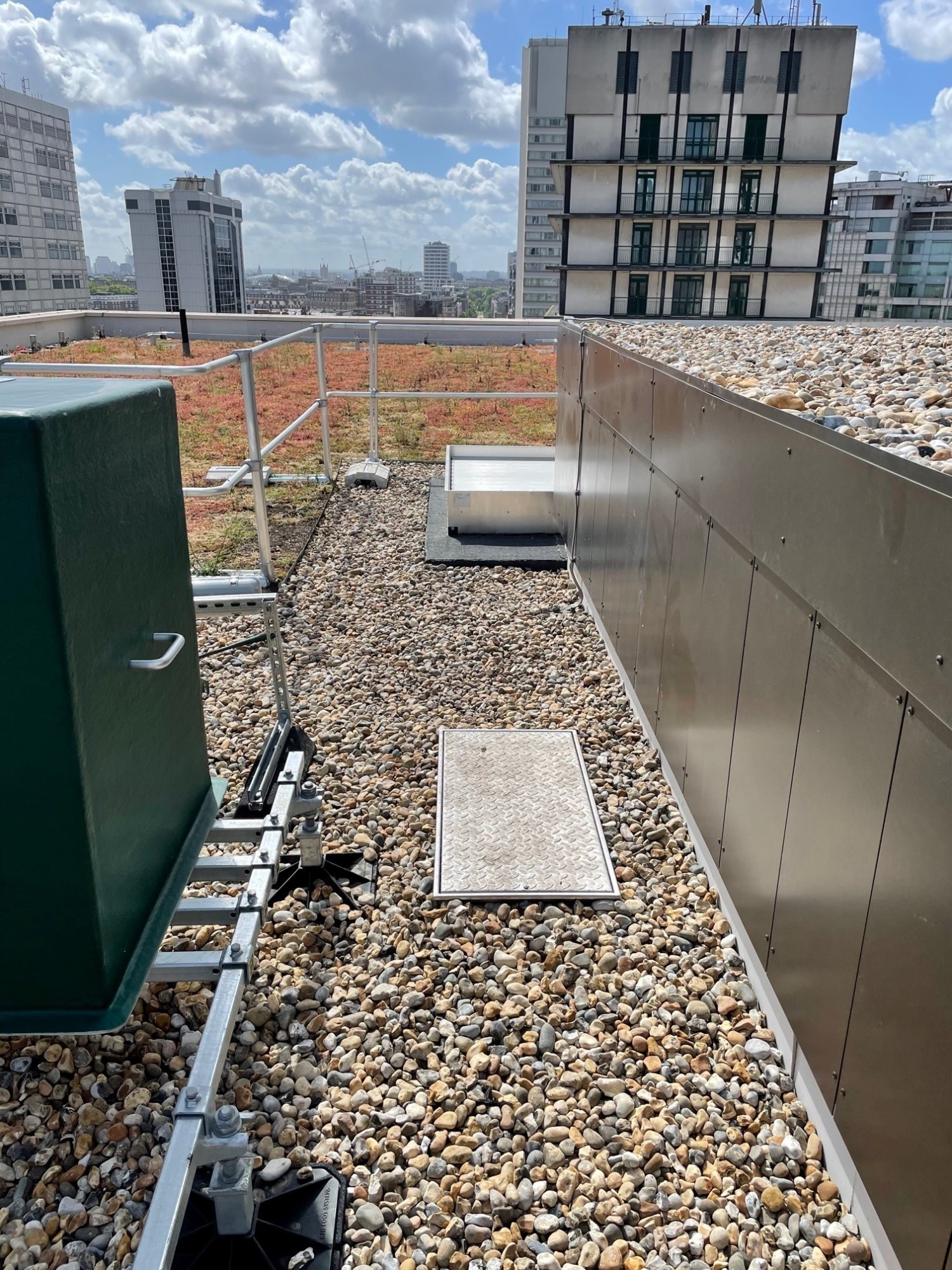
The team at Axter are all knowledgeable and expert in their field, so it makes good sense to involve them as early as possible in a project. They’re happy to investigate a number of different options, design innovative solutions and look after any technical detailing that may be required to ensure the most appropriate roof system is specified. This ‘right first time’ principle reaps benefits as the overall project moves forward, saving time and eliminating potential pitfalls before they occur.
Kevin Leahy, Technical Director, Berkeley Homes
Systems Used
Phase |
Blocks |
Systems used |
1 |
A-D |
Wilotekt-Plus, Force 4000, Force Dalle, Aquamodul |
2 |
E-F |
Wilotekt-Plus, Force 4000 |
3 |
G-H |
Wilotekt-Plus, Force 4000 |
4 |
I-K |
Wilotekt-Plus, Force 4000, Force Dalle, Aquamodul |
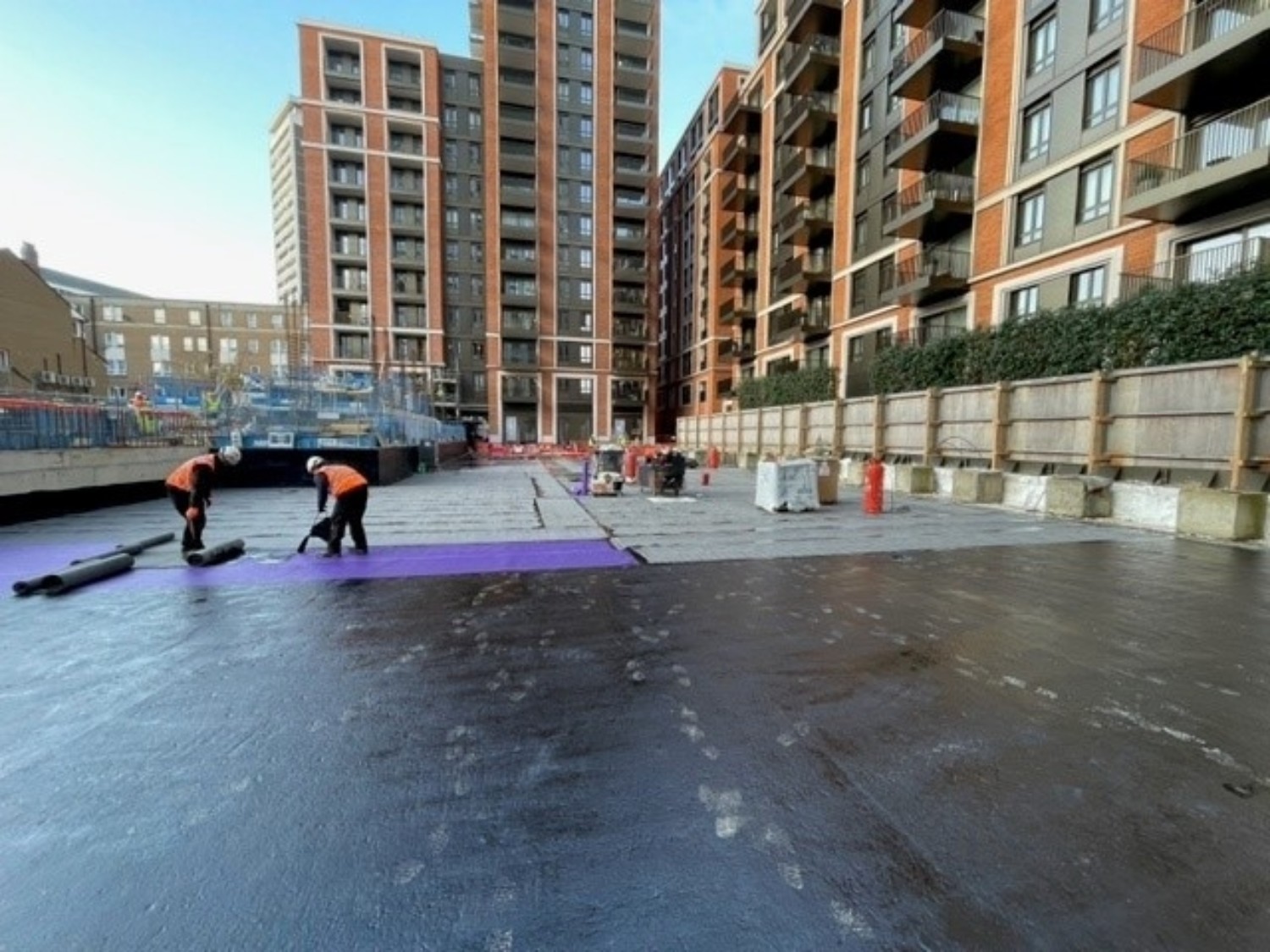
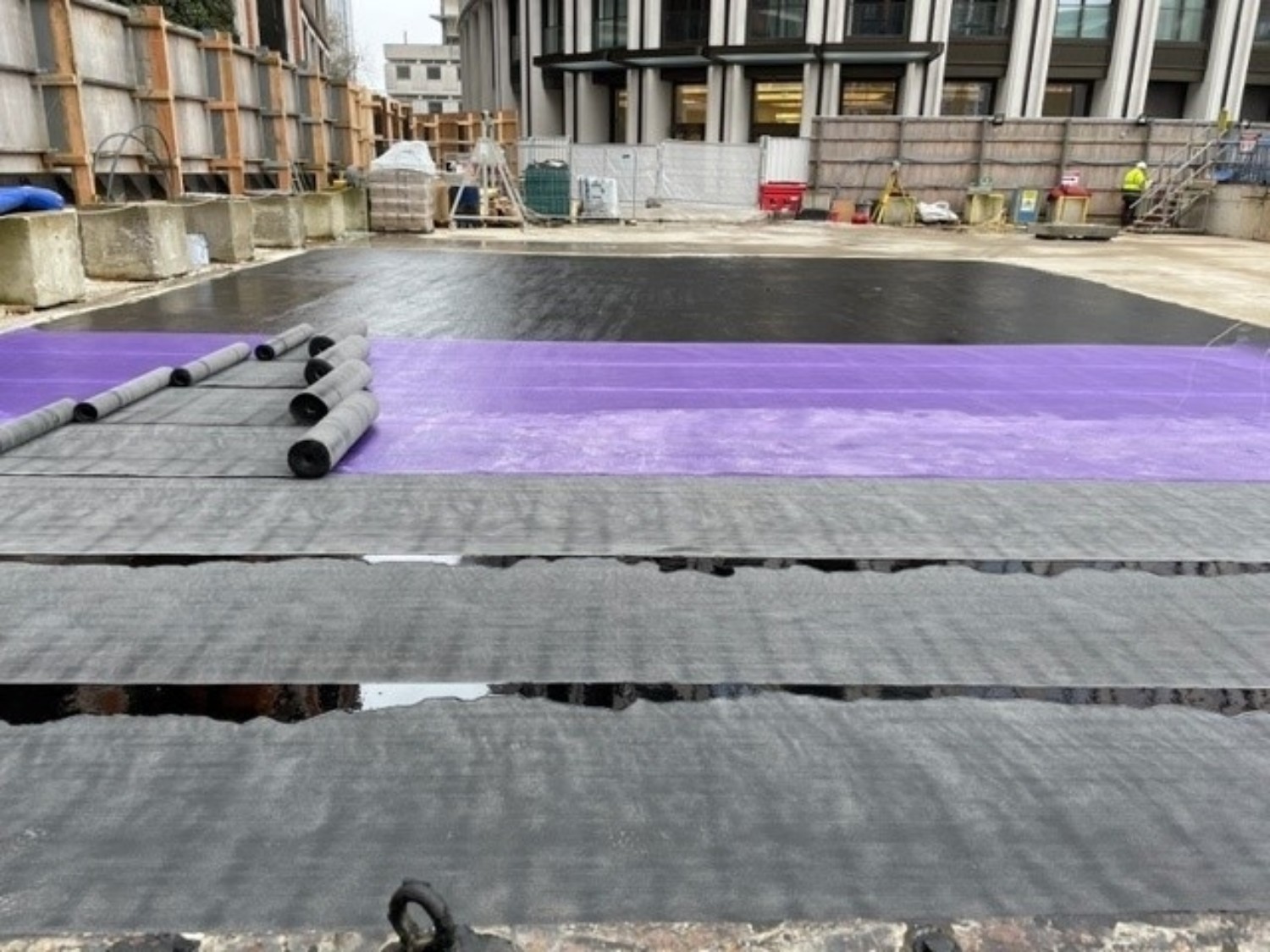